The client, a research facility, seeks to advance the understanding of our universe by providing laboratory space deep underground where highly sensitive physics experiments can be shielded from cosmic radiation. This laboratory space is located nearly one-mile (4,850 feet) underground and hosts of several individual facilities for various types of research.
The research facility required the installation of a new cleanroom to provide a dust and particulate-free environment in order to protect sensitive research equipment and data. Since its location underground added extra challenges to its installation, our distributor stressed the value of modular construction due to the ease of coordination through minimizing the numerous other trades which would typically be required to build with traditional construction. Acknowledging these advantages, our client decided to use modular construction for the installation of the new cleanroom.
Project Overview
Application: Underground Cleanroom Environment
Product: OmniFlex 11' Tall with Steel/Poly/Steel Panels
Benefits Provided:
- Thermal control to protect expensive research equipment
- Dust and particulate-free environment to minimize the possibility of contamination
The Challenge
After specifying the project, our distributor worked closely with the client to facilitate the transfer of building supplies to the installation site, 4,850 feet below the earth. This phase of the project proved to be the most challenging, due to the amount of time that was required - The only entrance to the site consisted of an 11-minute elevator ride down through an old mine shaft to deliver the supplies, and a 15-minute ride back up to the surface.
Our distributor took every precaution to ensure safe delivery of our modular systems during this delivery time, successfully avoiding any defects or compromises to the building’s components.
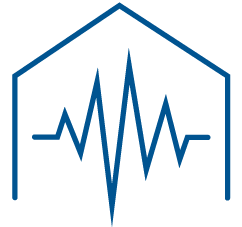
The Solution
Our distributor successfully installed the new cleanroom environment with minimal challenges, despite its location nearly one-mile below the Earth’s surface. The resulting enclosure provided our client with a temperature-controlled environment featuring a single-pass airflow design that minimizes dust, dirt and other potential sources of contamination. Despite the slow-process of transferring building supplies to the installation site, this project was completed on time and under budget.
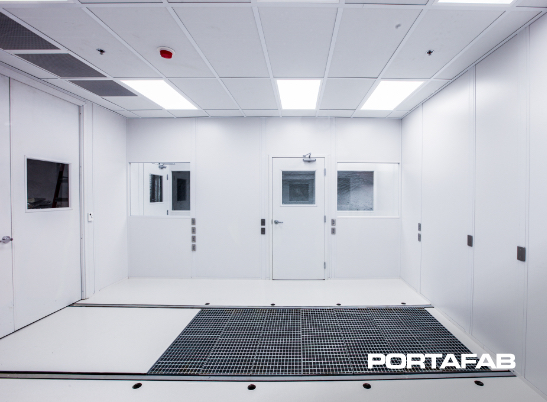