Table of Contents
ISO Cleanroom Standards
Companies that are required to comply with particular cleanroom design standards should be aware that cleanrooms can be constructed and managed to meet various levels of cleanliness classifications, depending on the specific environmental conditions necessary for their intended application. The International Organization for Standardization (ISO) is the main governing body responsible for establishing cleanroom classifications.
ISO 14644-1 Cleanroom Classification Table |
|||||||
Class |
maximum particles / m3 |
FED STD 209E |
|||||
≥0.1 µm |
≥0.2 µm |
≥0.3 µm |
≥0.5 µm |
≥1 µm |
≥5 µm |
||
ISO 1 |
10 |
2.37 |
1.02 |
0.35 |
0.083 |
0.0029 |
|
ISO 2 |
100 |
23.7 |
10.2 |
3.5 |
0.83 |
0.029 |
|
ISO 3 |
1,000 |
237 |
102 |
35 |
8.3 |
0.29 |
Class 1 Cleanroom |
ISO 4 |
10,000 |
2,370 |
1,020 |
352 |
83 |
2.9 |
Class 10 Cleanroom |
ISO 5 |
100,000 |
23,700 |
10,200 |
3,520 |
832 |
29 |
Class 100 Cleanroom |
ISO 6 |
1.0×106 |
237,000 |
102,000 |
35,200 |
8,320 |
293 |
Class 1,000 Cleanroom |
ISO 7 |
1.0×107 |
2.37×106 |
1,020,000 |
352,000 |
83,200 |
2,930 |
Class 10,000 Cleanroom |
ISO 8 |
1.0×108 |
2.37×107 |
1.02×107 |
3,520,000 |
832,000 |
29,300 |
Class 100,000 Cleanroom |
ISO 9 |
1.0×109 |
2.37×108 |
1.02×108 |
35,200,000 |
8,320,000 |
293,000 |
Room air |
(µm denotes micron particle size)
What is a cleanroom according to the ISO standard 14644?
ISO 14644-1 classifies a cleanroom based on the size and number of airborne particles per cubic meter of air (see chart above).
Prior to the implementation of ISO 14644-1, US Federal Standard 209E set the industry guidelines for cleanroom classification, and denoted the number of particles 0.5µm or larger per cubic foot of air. For instance, under FED-STD-209E, a "class 1000 cleanroom" would indicate 1,000 particles 0.5 µm or smaller in each cubic foot of air. FED-STD-209E was officially cancelled on November 29th, 2001, though both standards are still widely used.
The cleanroom you may need is going to be determined by several different factors:
- Industry Standards
- Government Regulations
- Customer Requirements
- Ease of Cleaning
- Restriction of Access
- Particulates
- Temperature
- Humidity
- Microorganism
Once all of these factors are considered, you can then make accurate choices regarding the scope of the cleanroom operation you should implement, or whether your operations would be better suited with a controlled environment instead.
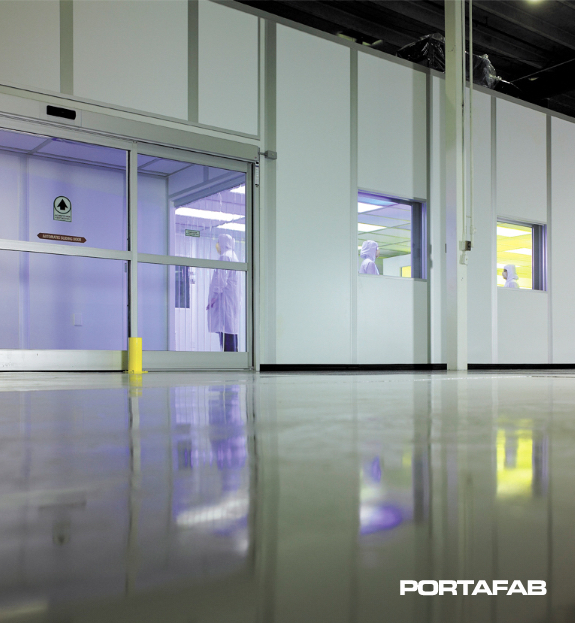
Video Resources
Cleanroom Considerations
When considering a certain ISO classification of cleanroom it is critically important to ensure that your operation’s needs align with the scope of the ISO level you select. For example, choosing a modular cleanroom that is more robust than the needs of your operation may make it difficult to meet the ROI of the cleanroom. Additionally, selecting a cleanroom that does not meet the needs of your operations can lead to the contamination of your products or services, which will incur further costs and may affect future customer relations. For examples of our cleanroom solutions in action, listed below are several cleanroom case studies.
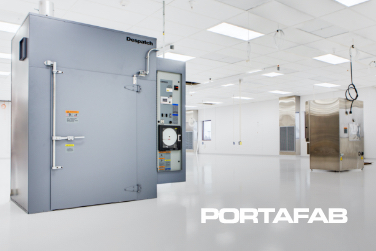
ISO 8 (Class 100,000) Cleanroom
A medical device manufacturer required complete environmental control with ISO 8 validation in order to completely contain one of their manufacturing processes.
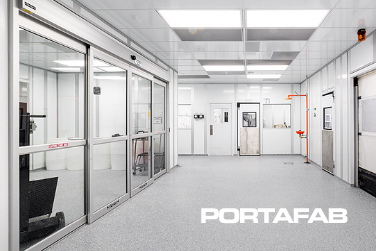
ISO 7 (Class 10,000) Cleanroom
A manufacturer required multiple clean environments in which to contain each stage of the manufacturing process from initial mixing to product packaging.
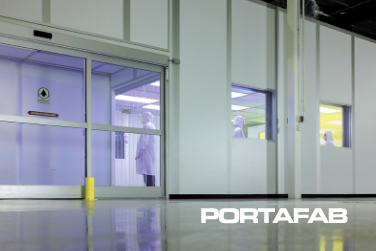
ISO 6 (Class 1,000) Cleanroom
Our customer required the quick creation of a modular cleanroom that would aid in their new cleaning service targeted at semiconductors, microelectronics, and medical products.
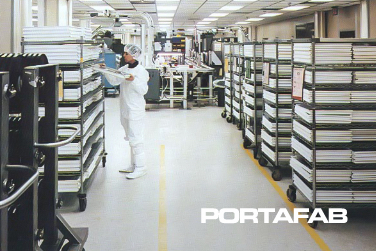
ISO 5 (Class 100) Cleanroom
A data and technology company required a high-quality yet flexible cleanroom to accommodate their expanding tape manufacturing operation.
FAQs
What are cleanroom requirements?
Cleanroom requirements are standards determined by a non-governmental organization (ISO: International Organization for Standards) that dictate air quality in a cleanroom, including a certain number and size of particles in a cubic meter.
What are the classes of cleanrooms?
Cleanrooms are classified according to the level of cleanliness they provide. The classification system is based on the number and size of particles permitted per volume of air, as specified in ISO 14644-1. The classes of cleanrooms are Class 1, Class 10, Class 100, Class 1,000, Class 10,000, and Class 100,000.
What are ISO standards for cleanrooms?
ISO standards for cleanrooms are a designated set of requirements for filtering the size and quantity of particles in an enclosed area. The standards range from a designation of ISO 1 through 8, and the amount and size of particles in the air increase as the classification advances from 1 (lowest number and size of particles) to 8 (highest number and size of particles). An ISO class 9 designation exists, but there is no control on particle size at this class, only the quantity.
Which ISO cleanroom class is the cleanest?
ISO Class 1 is the cleanest cleanroom class, allowing only up to 10 particles greater than or equal to 0.1 microns in size, in a cubic meter of air.
What class is ISO 14644?
ISO 14644 is not a cleanroom class, but a standard that specifies the requirements for cleanrooms and associated controlled environments. It provides guidelines for the design, construction, operation, and monitoring of cleanrooms to ensure the desired level of cleanliness is achieved and maintained.
How Contamination Relates to Cleanroom Classification
A typical cleanroom is designed to keep the outside environment from getting in. Once an environment has been built, the two things that cause contamination in it are the people and the process. Understanding the contamination sources and combating those with solid cleanroom design and enhanced operations can provide significant cost savings from both construction and operational standpoints.
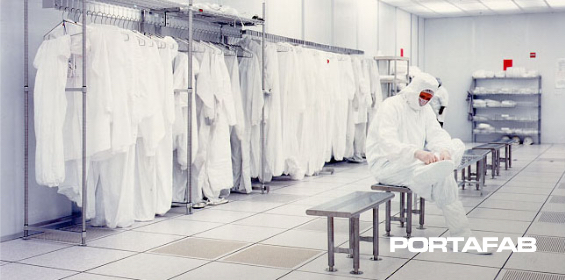
Proper Garmenting
Often times one can build a lower classification of cleanroom, though still maintain a cleaner environment by enhancing operations within the cleanroom - for instance, garmenting workers to a higher standard.
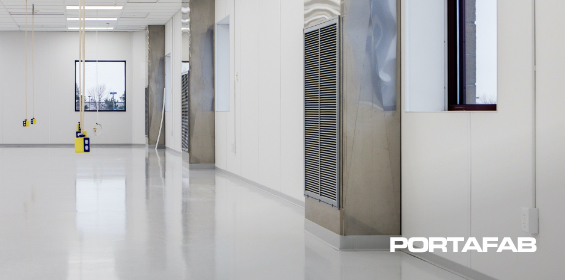
Air Control
Positioning return air grills and filtration systems at optimal locations within the cleanroom can result in cleaner areas within the environment, thus bringing the cleanroom classification to a lower level in those areas.
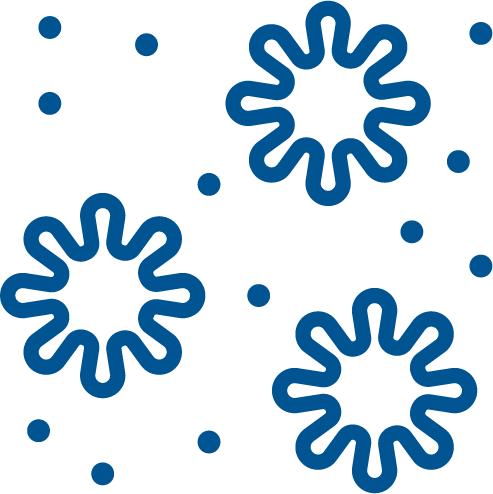
How Particle Size Impacts Classification
One of the most important factors to determine when constructing a cleanroom is what size of particle will need to be filtered out. Is it any size particle? Is it a specific size or range of particles? Often times, people look at the cleanroom classification (see chart above) and they go to the lowest level particle count to determine what classification they need.
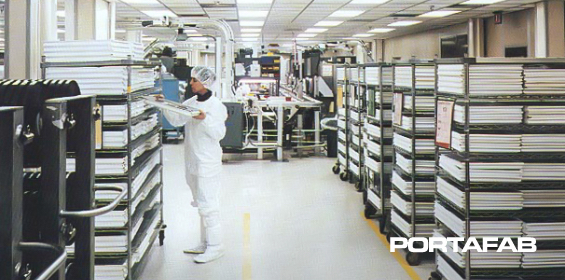
How to Choose the right ISO Level
An example of this would be someone that determines they need less than 100 particles per square foot within their cleanroom. Based on this information, they determine that the classification will need to be an ISO 5 (or class 100) cleanroom. However, an issue can arise if they do not take into account the size of the particle they are trying to filter out.
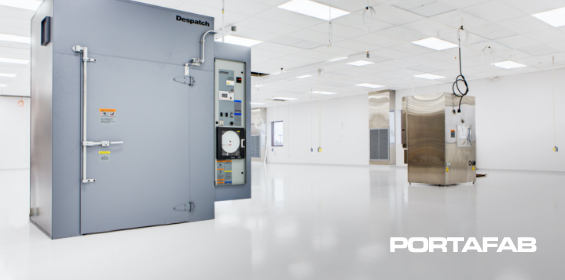
Micron Size can determine ISO Level
There’s a significant difference in the classification that is needed if that particle is 1/2 micron in size versus 5 microns in size (see Micron description below). If they think they’re looking at a ½ micron sized-particle, but really the particle that is a problem for them is a 5 micron particle – From a cleanroom classification, this doesn’t translate to an ISO 5 cleanroom (or class 100). This actually translates into an ISO 8 cleanroom (or class 100,000).
In the cleanroom environment, air particles are measured in microns. One micron equals one-millionth of a meter. Micron-sized particles are smaller than a living cell and can be seen only with the most powerful microscopes.
To put this in perspective, a strand of human hair can vary in width from approximately 20 to 180 microns, while the average size is typically 50-70 microns.
- One small dust particle seen in a ray of sun equates to approximately 60 microns.
- The human eye cannot consistently see objects less than 50 microns in size.
- Pollen is approximately 30-50 microns.
- Bacteria are approximately 2 to 10 microns in size.
- A typical indoor air sample may contain anywhere from 500,000 to 1 million particles per cubic foot of air.
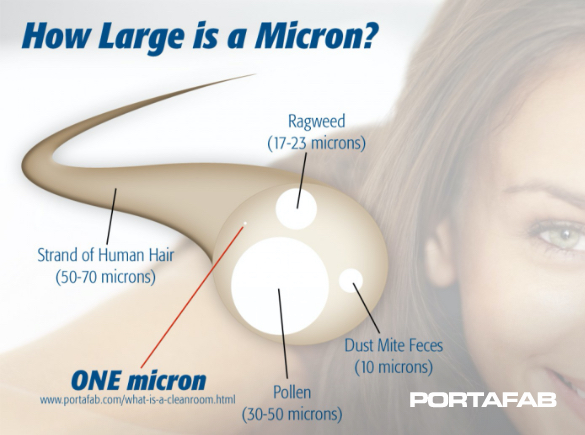
By comparison, an ISO class 5 cleanroom is designed to allow no more than 3,520 particles equal to or larger than 0.5 microns per cubic meter of air. This equates to a Class 100 cleanroom under the Federal Standard 209E, which allows for 100 particles (0.5 microns or larger) per cubic foot of air.
How Air Circulation Affects Classification
Any time the classification goes down a class, or up a class - for instance from an ISO 8 (class 100,000) to an ISO 7 (class 10,000) - that’s going to take twice as much air. The cost of filtering and moving air is a significant cost of operating a cleanroom. This process translates all the way down through to the number of filters that are needed, the amount of return air space that is needed, the amount of air conditioning that will be needed to cool that return air and so forth. And this multiplies itself as one goes through the process.
A common mistake involves a client asking for a cleanroom that is too tall, or otherwise in excess of what they really need. If you require a cleanroom with an 8-foot ceiling height, but decide to make it taller in order to align better with the surrounding environment and make it 10-feet high, that changes the volume of the area by 25%. Therefore they’re increasing the amount of air needed for that cleanroom by 25% because they decided on building a 10-foot height, when they only needed an 8-foot height.
What would seem to be a simple difference (moving from one class to the other) significantly changes the cost of a cleanroom - almost 25% for the same sized cleanroom at the same classification.
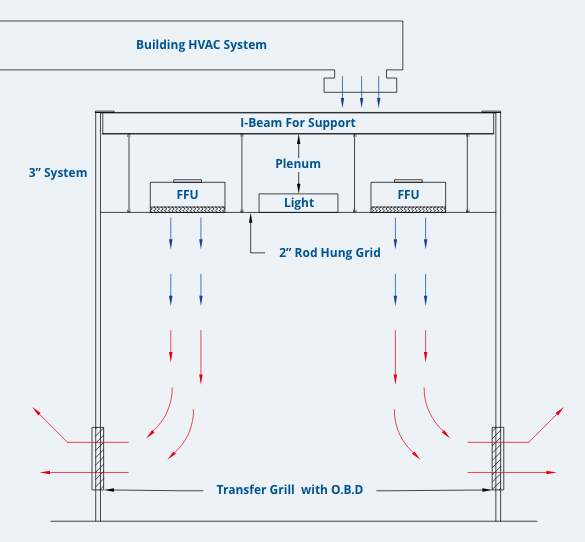
Controlling Temperature, Humidity, & Airflow
Controlling the environment within a cleanroom is critical to the success of a cleanroom and operations that take place within it. Provided below are two videos that go into further depth regarding controlling a cleanroom environment.
Save Costs with a Controlled Environment
One of the reasons for the development of the ISO standards was to accommodate an environment called “ISO Class 9” which was never a cleanroom classification before. This classification translates roughly into what the pharmaceutical industry calls a “controlled and classified area.”
By controlled and classified, this means that it is controlled to a particle level (via HEPA air filtration), its controlled to the temperature and humidity that has been specified, but it’s not classified in terms of the particle count. A “controlled and classified area” is pressurized, it features temperature control and the air is filtered. It is just not specified in terms of the amount of and size of particles within a given volume of air.
In many cases, this type of environment is all that a client needs in terms of a “cleanroom”. If a company is not careful, they can end up building a cleanroom far beyond their actual requirements and there are dramatic costs involved with doing that.
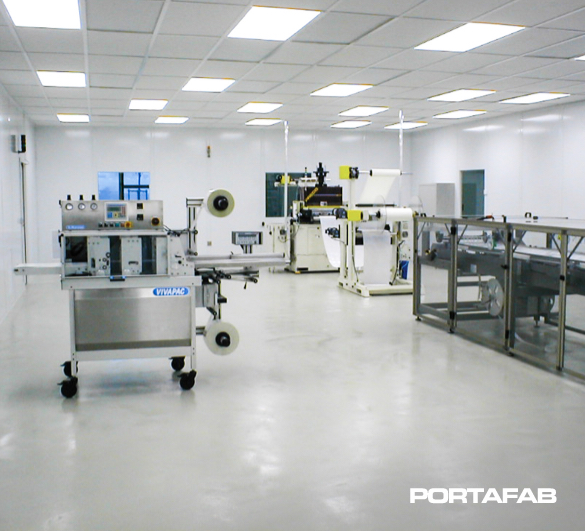