Our client, a prominent player in the storage and handling solutions sector for the microelectronics industry, embarked on a new venture to leverage their cutting-edge cleaning technology and extensive expertise. Recognizing a rising demand in the market for cleaning services catering to sensitive semiconductor, microelectronics, and medical products, they aimed to seize this opportunity and establish a specialized business focused on fulfilling these requirements.
Project Overview
Application: 1,000 Square Foot - Class 1000 / ISO 6 Cleanroom
Product: CleanLine S3000 with Flush Windows
Benefits Provided:
- Speed of completion
- Corporate showpiece for attracting new business
The Challenge
Our client needed a customized cleanroom that could be quickly and efficiently constructed in order to get the new company up and running. Cleaning and drying equipment needed to interface seamlessly with the structural components and all windows needed to be flush with the wall to minimize any hidden areas for particulate. It also had to have a load bearing roof so that air filtration systems and other equipment could be mounted on the cleanroom envelope and not take up valuable space in their new facility. While they expected this business to grow rapidly, they still wanted to start small and utilize modular components that would allow them to expand without significant additional costs.
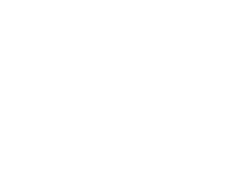
The Evaluation
Our client chose a modular cleanroom system from PortaFab that could be easily customized to fit their exact requirements and provided a cost-effective alternative to conventional construction. The modular system could also be built more quickly and would allow them the future flexibility they desired.
"When I began the development of this cleanroom, I described the client's process, detailed their specifications, and sent a rough sketch. PortaFab's engineers then prepared drawings and outlined the exact components needed to construct the cleanroom. This wasn't a cleanroom kit - all components including the air filtration and humidity control systems, doors, windows, equipment storage and more were seamlessly integrated into the cleanroom design from the start."
- PortaFab Distributor
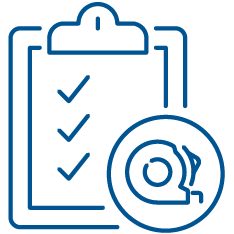
The Solution
The end product was a 1,000 square foot, class 1000 cleanroom that utilized PortaFab's CleanLine S3000 all aluminum stud system along with flush windows and aluminum/vinyl hardboard composite wall panels. It includes a main work area, a gowning room and an equipment room and provides effective control of air flow, pressure, temperature, humidity and filtration.
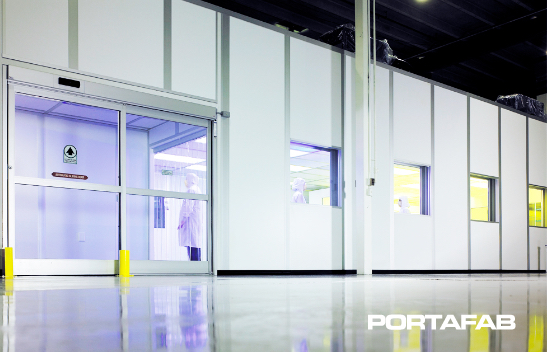

The Results
From the date of first contact, the cleanroom was completely finished in about six months and our client was able to launch its new cleaning services without any issues. Plus, the attractive high-tech look of the new class 1,000 cleanroom made it a showpiece for potential customers. The aluminum stud and wall systems created this impressive look that interfaced seamlessly with floors, ceilings and mechanical components to provide an ultra-clean environment.
Since its completion, the cleanroom has helped our client achieve significant business growth and to expand its business in the semiconductor, solar, optical, and medical industries. In fact, the versatility of the cleanroom facility has them anticipating additional growth in the coming year.
"The class 1000 cleanroom has now become a showcase for all of our affiliate companies. Because of its pristine condition, we bring all potential customers through the facility in order to demonstrate our credibility in the industry. I am glad we decided to go with a modular cleanroom because we are already operating near the full capacity of this cleanroom and the modular nature of the PortaFab systems will allow us to expand easily."
- Client testimonial