Even though our modular cleanroom systems can be used to create highly-advanced critical environments, this type of application is typically a smaller percentage of the cleanroom market that we serve. The majority of our products are used by manufacturers seeking to adhere to current GMP (good manufacturing practices) and standards through the use of quality control rooms, also known as "GMP rooms".
Modular Wall System for GMP Rooms
Our modular wall systems are ideal for building GMP rooms to house machinery, safely store equipment, contain specific processes and other end-applications including:
- Quality Control & Inspection Rooms
- Machine & Equipment Enclosures
- Sensitive Goods & Equipment Storage
- Powder Coating Enclosures
- Industrial Paint Application Rooms
- Packaging & Printing Areas
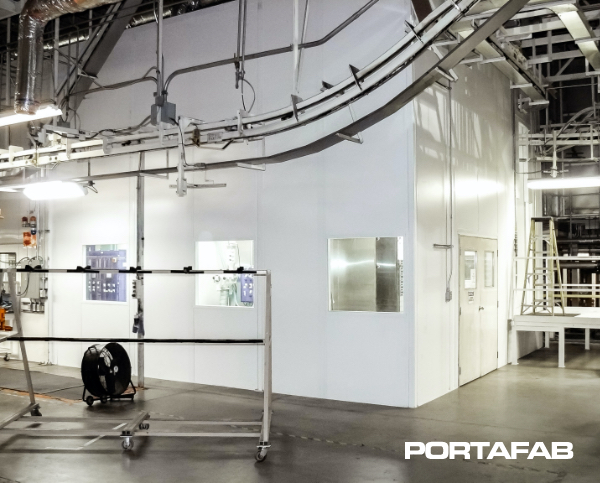
Do you need to maintain greater control over environmental conditions like air quality, humidity and temperature? Manufacturers in various industries have utilized PortaFab's modular systems to create GMP rooms that will;
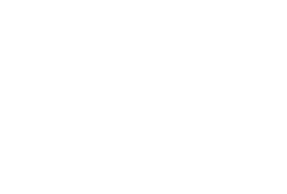
Help improve product quality
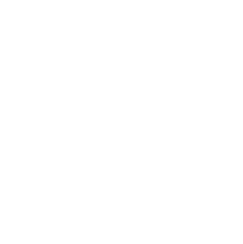
Maintain process consistency
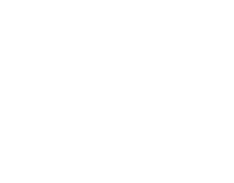
Increase product yield
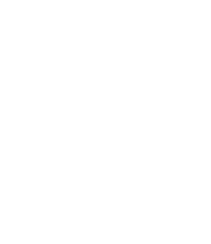
Enhance safety and security
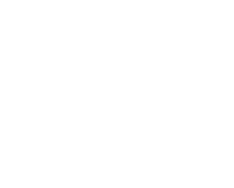
The Modular Advantage
Our wall systems and components provide a wide-range of benefits due to their modular design and non-progressive nature including:
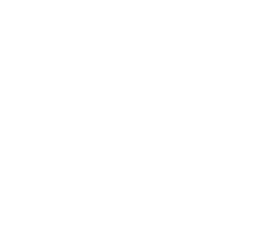
Reduced labor costs
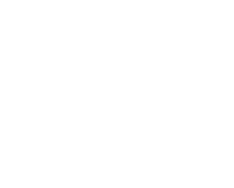
Quick and clean installation
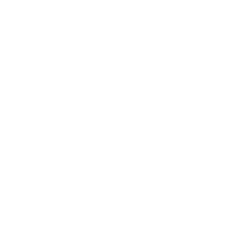
Low mess
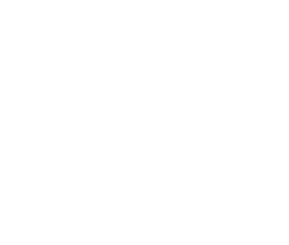
Tax advantages
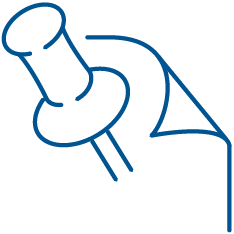
Case Studies
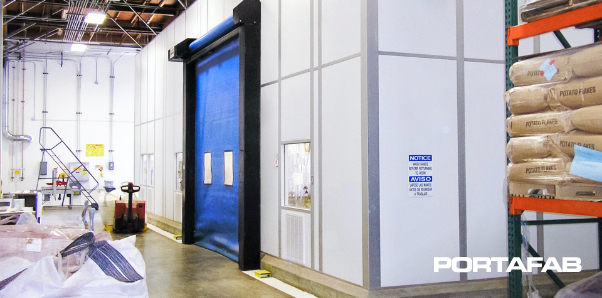
Case in Point #1
Felbro Food Products, Inc. manufactures over 600 different line items, including gourmet sauces, soup bases, pancake syrups, flavorings, extracts and food colorings. When Felbro acquired a new facility, the concern for contamination and mold growth during the food processing development was high. They needed a cleanroom that would not only limit contamination from outside sources, but also allow for extensive cleaning. The benefits provided:
- Quality control
- USDA compliance
- Improved product yield
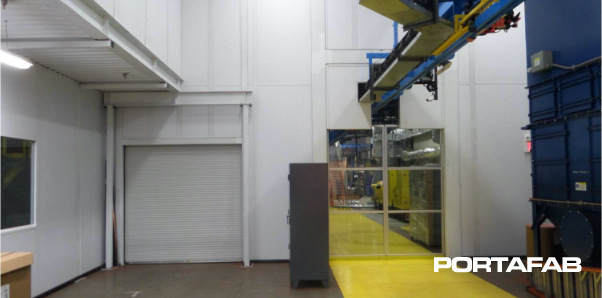
Case in Point #2
Bobcat is a known leader in the design, manufacture, marketing and distribution of compact equipment for construction, rental, landscaping, agriculture, grounds maintenance, government, utility, industry and mining. In order to maximize operational efficiency, our client required the installation of an environmental room at their headquarters in order to contain the processes and equipment used in paint finishing and coating applications. The benefits provided:
- Effective environmental control
- Timely installation with minimal disruption to plant
- Met 24’ height requirements
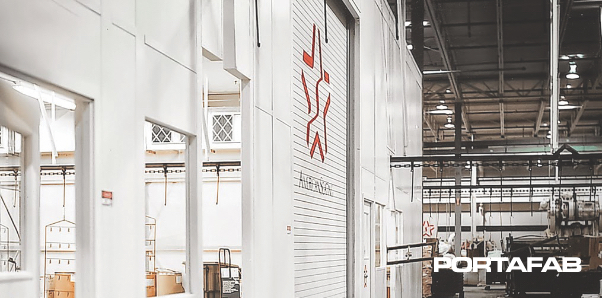
Case in Point #3
American Seating's world class manufacturing facility in Grand Rapids, Michigan was undergoing changes and needed and environmentally controlled application room to enclose their powder coating process. Due to the precise nature of the powder coating process, it was important to maintain temperature and low contamination conditions within the room while preventing dust particles and other contaminants from entering. The benefits provided:
- Effective environmental control
- Effective sound control
- World class appearance