PortaFab’s distributor identified a potential opportunity for modular construction through researching local construction bulletins. The project involved the creation of a new containment area which would be used for mixing and bottling of baby formula by a worldwide Fortune 200 company.
A general contractor had already been awarded the project and was planning on using conventional construction to construct the enclosure. In response, our distributor was proactive in contacting the general contractor to discuss an alternative solution for the enclosure through modular construction. After discussing modular solutions with the contractor and researching competing modular companies, the client settled on PortaFab’s modular systems based on the better price.
Project Overview
Application: Containment Area for Mixing & Bottling Baby Formula
Product: PortaMax Aluminum System Featuring Epoxy-coated Aluminum Panels (Fire and Sound) with Moisture-Resistant Gypsum (17’4” - 20’ tall because of the ceiling truss)
Benefits Provided:
- Epoxy-coated surfaces comprised of moisture-resistant gypsum to withstand water penetration during cleaning process.
- Floor to ceiling wall system seated upon 6-inch high curb (to contain excess water during wash down).
- Seamless integration of walls with existing conveyor system, concrete columns and trussed ceiling.
The Challenge
The layout of the existing facility provided a few key challenges to our distributor. First, the walls would need to extend to the ceiling structure for seamless containment. Since the existing roof structure featured concrete trusses perpendicular to the wall system, there was the added challenge of attaching the walls to a range of uneven heights. The existing layout also featured four columns extending from the ceiling to the floor, which the walls needed to connect to, furthering the custom arrangement of our modular wall system.
Our distributor took great care in attaching the proper connections and applying the correct angles to ensure a seamless structure was installed. The enclosure would also need to be integrated with the existing conveyor system to provide a seamless transition between processes. Our distributor worked in conjunction with PortaFab engineering, providing detailed drawings during the approval process to ensure successful installation of our modular systems.
The Solution
Due to the cleaning protocol within the containment area, there were concerns about moisture penetrating the wall system. In response, our distributor recommended using epoxy-coated aluminum wall surfaces, stainless steel window frames, caulking around all joints and utilizing moisture-resistant gypsum coating to reduce the potential for wall panel deterioration or contamination. The walls surrounding the containment area were also installed upon a 6-inch high curb, which helped contain excess water during wash down and cleaning processes.
The resulting installation provided the client with a new containment area featuring water-resistant wall structures that extended from the floor to the ceiling, while also seamlessly connecting from the concrete curbs to the trussed roof and across 4 concrete columns. Finally, the new containment area successfully integrated with an existing conveyor line to enhance operational throughput.
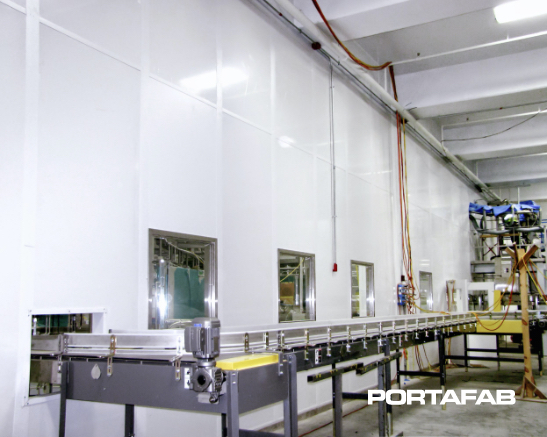