A major provider of products and systems for semiconductor device fabrication required the installation of a modular cleanroom environment in which to safely package wafers for transportation. The cleanroom would require various ISO classifications in order to retain material purity and to ensure safe transport of wafers to clients within the industry.
Project Overview
Application: Decontamination Room
Product: Series 300, Aluminum Fire & Sound Panels
Benefits Provided:
- Airtight chamber with panelized roof and interlocking door systems
- Epoxy-coated surfaces to withstand cleaning and decontamination agents
- Rigorous testing and qualification processes prior to project approval
The Challenge
The enclosure needed to fit several requirements in order to fulfill its intended purpose. To meet these requirements our distributor worked closely between the client and PortaFab’s engineering department to develop a highly customized solution.
First, our distributor made an initial site survey to gather the required information and standards for this project. The enclosure needed to provide an airtight environment that could withstand rigorous cleaning and sterilization agents and processes. After consulting with the client and PortaFab engineering, our distributor provided samples of PortaFab’s modular components to demonstrate their capabilities and allow them to be tested by the client.
Once the wall panels and framing system were approved, mock-ups were provided to the client so that they could test the materials and confirm the exact standards and requirements would be met.
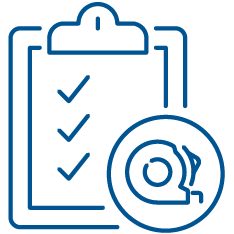
The Solution
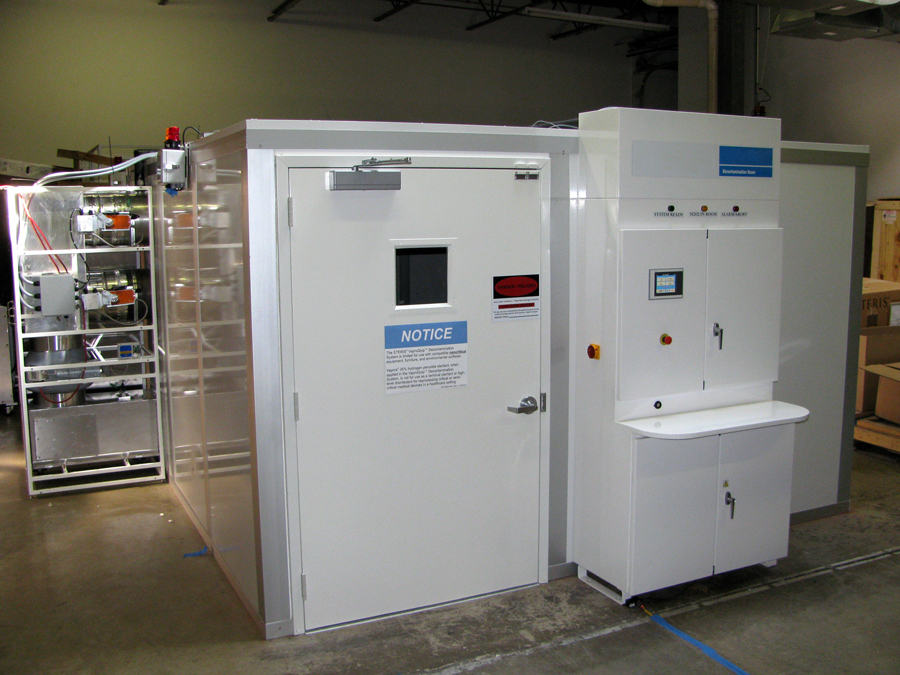
Through the discovery process with the client and PortaFab engineering, it was determined that the Series 300 aluminum framework with epoxy-coated aluminum wall surfaces would provide the best solution. These components would provide an airtight environment that was also impervious to penetration by sterilization and cleaning agents.
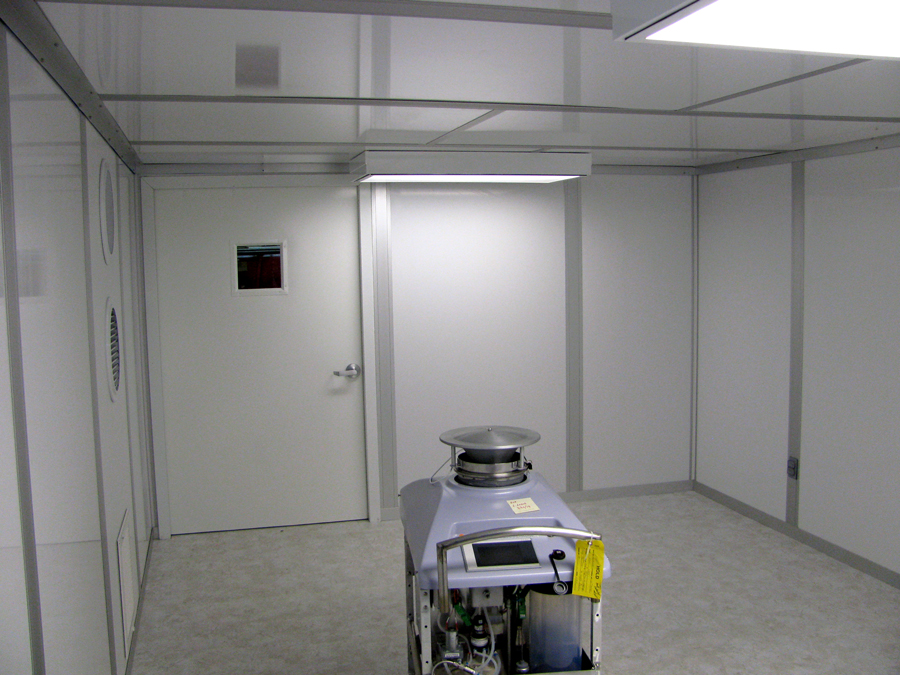
The new enclosure featured a panelized roof that was made from the epoxy-coated aluminum wall panels, creating a seamless surface from ceiling to wall. The access door to the enclosure also featured interlocking systems to ensure an airtight enclosure, while the epoxy-coated surfaces would provide the necessary protection from the sterilization processes inside. A small window featured on the access door provided a view inside the enclosure to allow for monitoring and inspection of the process inside.